Innovazione
giovedì 17 Novembre, 2022
I seggiolini da giostre del futuro si fanno a Rovereto
di Redazione
Le nuove sedute hanno un peso dimezzato che consentirà di avere strutture più leggere, minore usura e minori sollecitazioni con conseguente riduzione dei costi e risparmio energetico
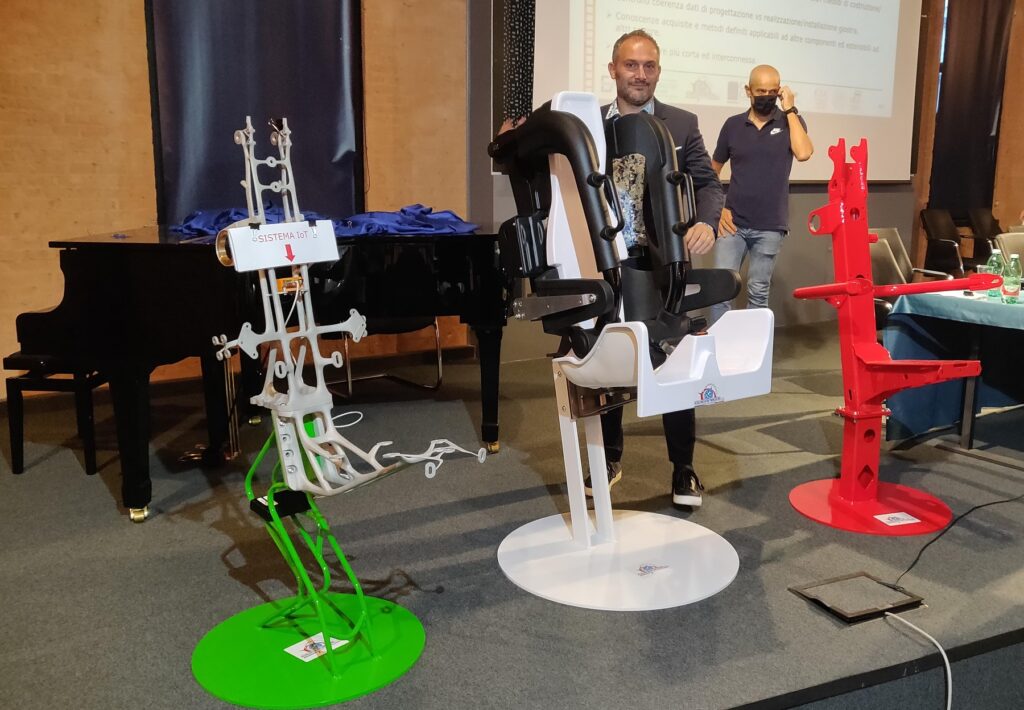
Diventerà oggetto di un paper scientifico il nuovo seggiolino da giostra prototipato nel laboratorio ProM Facility di Trentino Sviluppo in Polo Meccatronica a Rovereto. Grazie alla maggiore libertà geometrica consentita dalla fabbricazione additiva, il peso del telaio metallico del seggiolino di una giostra a pendolo, che può compiere rotazioni a 360 gradi e ospitare fino a 32 passeggeri, è stato praticamente dimezzato, passando da 36 a 17 chilogrammi. Avere delle parti in movimento più leggere permette di ridurre a cascata anche tutto il resto della struttura, che sarà meno sollecitata. Ma non solo. Anche i motori, i freni e il consumo elettrico dell’attrazione diminuiranno, permettendo ai giostrai e ai gestori di luna park e parchi tematici di essere meno esposti al caro bollette.
Il progetto è stato finanziato nell’ambito del bando POS-FESR 2014-2020 della Regione Veneto e ha visto coinvolti, oltre al laboratorio ProM Facility di Trentino Sviluppo e all’impresa Extreme Analyses Engineering, in qualità di capofila, anche la società Guarnieri, costruttrice di attrazioni per parchi di divertimento e spettacoli viaggianti, il Parco Scientifico Tecnologico di Verona, l’Università di Padova, l’Officina Meccanica Claudio Cioetto e la società Exemplar, specializzata in sviluppo software per la simulazione virtuale e partner certificato di Dassault Systems.
Il progetto, denominato M.P.M.A.G, acronimo di «Metodo di Progettazione e Produzione in Additive Manufacturing di componenti complessi del settore delle Giostre», consisteva nel trovare un sistema per rendere le parti mobili delle giostre – ovvero le sedute – più leggere ed efficienti grazie alla manifattura additiva. La maggiore libertà geometrica della fabbricazione additiva ha consentito infatti di diminuire il peso del telaio metallico del seggiolino di una giostra a pendolo, che può compiere rotazioni a 360 gradi e ospitare fino a 32 passeggeri.
«Rispetto ai 36 kg della struttura in carpenteria saldata – spiega Simone Bernardini, amministratore delegato di Extreme Analyses Engineering – la struttura in acciaio inox si ferma a circa 17 kg. Dimezzare il peso delle parti in movimento della giostra permette a cascata di ridurre anche tutto il resto della struttura, che sarà molto meno sollecitata per via delle minori masse. Infine, anche i motori, i freni e il consumo elettrico per tutta la vita dell’attrazione saranno minori rispetto che alla versione classica».
La lavorazione, brevettata, è stata volta in ProM Facility con la macchina ibrida Lasertec 65 3D di DMG MORI. I tecnologi del laboratorio Matteo Perini e Ciro Malacarne raccontano: «La produzione dei pezzi ha richiesto circa 80 ore di deposizione effettiva per 60 kg di polvere di acciaio con diverse ore dedicate all’ottimizzazione dei percorsi CAM del controllo numerico. È stato inoltre necessario rivedere il design della seduta considerando che ogni pezzo viene realizzato per deposizione di materiale su piastra sacrificale, dalla quale viene separato mediante elettroerosione a filo dopo trattamento termico di distensione delle tensioni residue indotte dal processo additivo».
Concluso il progetto con successo, si apre ora per i tecnologi di ProM Facility la fase di scrittura di un paper scientifico, finalizzato a dimostrare la sostenibilità della stampa additiva applicata al mondo delle giostre.
Grandi opere
Nuova galleria nella (gloriosa) strada del Menador: avviata la gara da 8,5 milioni. «Interventi per migliorare la sicurezza»
di Redazione
Le due gallerie storiche attuali saranno mantenute e adibite a senso unico in salita, snellendo il traffico soprattutto nei periodi di maggiore afflusso